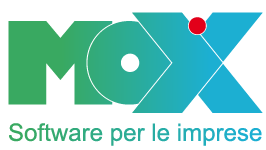
Mox Solutions Srl
https://www.moxsolutions.it

Information related to the company
Company description
MOX SOLUTIONS S.R.L. arose in 2006 from a business idea which aims to ensure fast solutions (hence the name MOX, that in latin means “rapid”) of high-quality software integration. The proposed software solutions stand out in business software for their high technology and quality, thanks to the professional experience that the collaborators have gained in the logistics management, production management and sales processes.
The answer of the Mox Solutions team, is based on the concept of integration of pre-existent software. This mission is accomplished by providing the customer with expert consultancy from the Mox staff, with clear indications on how much work should be performed to ensure the integration and the optimization of pre-existent business processes with the WMS system.
Some numbers:
- 21 collaborators including employees and professionals
- 84 Stockforce WMS logistics installations
- 35 "light" logistics installations
- Installations present throughout Italy and Europe (Germany, UK).
History
Mox Solutions, located in Castelfranco Veneto (TV) - Italy, has been operating since 2006 and is the result of the convergence of a multi-year expertise of the 3 founding partners in the field of business software and the integration of software systems, combined with the sharing of approach methodologies in the resolution of enterprise issues, in the IT field.
The shared company vision led the company, in 2007/2008, to commercialize software products on mobile devices orientated to logistics and management of internal flows of goods in warehouses, with an innovative and modern solution.
The use of heterogeneous devices, typically but not exclusively Microsoft's mobile operating systems, does not limit the proposed solution, which is very flexible.
In 2008 MOX extended its product range with a project aimed to manage and collect factory data, a typical action in a Manufacturing Execution System, once again with the usual mobility characteristics.
In 2009-2010 MOX established reseller agreements (still active) for its logistics products with companies of national importance in the distribution of ERP systems and their distribution networks, which consist of more than 200 dealers.
In 2011 the three MOX partners founded Temovo s.r.l., extending the collaboration with other partners with specific commercial skills, always in the field of business software, with the aim of distributing products for the Sales Force Management using tablet technology. Specifically, they created SELLMORE, a Sales Force Automation App for iPad.
In 2013, MOX completed the drafting of a development framework that was able to generate multi-platform web applications (Microsoft, Apple, Android) from which specific solutions on companies wireless systems have been developed, specifically for production control in the different departments (management of the processing cycle, order progress, materials withdrawal, etc.).
In 2015 MOX released the first version of the new Stockforce WMS, with web interface for the management and control of logistics flows and extended its customer base specifically in the food industry where it met and responded to the specific needs of this type of industry in terms of batch management, traceability, management of the shelf-life, etc.
In the three-year period 2016-2018, MOX further enhanced the Stockforce suite by expanding its functionalities with a system able to do evadibility analysis of the order portfolio and able to give, in a proactive way, delivery dates relying on real-time incoming requests by customers and inventory changes. At the same time, it reached and exceeded the 100 served client companies with the new WMS solution, consolidating the experience in different specific industries such as pharmaceuticals, cosmetics and mechanics.
Information related to the product
Stockforce WMS 1.30.1
Description
Stockforce WMS manages the active, passive and transit flows of a modern warehouse, in a precise and flexible way. It quickly optimizes the operations of storage, movement, withdrawal, tracking of batches and serial numbers, increasing productivity and guaranteeing high quality logistics services to customers.
It is also provided with an innovative system for the fulfillment of the customer order portfolio available via web to optimize deliveries.
Some characteristics
- multi-company: for a separate but integrated management of multiple companies with different customers
- multi-warehouse: with a versatile factory management, multiple physical warehouses per factory, more logical warehouses per physical warehouse
- Notifications Management: in real time when monitored events occur (low level of item stock, new task, picking started/ended, etc.)
- Specific management for the Food&Beverage industry
- Departmental WMS: can be integrated with the ERP via already existing and compatible connectors
- Available in cloud for the distributed logistics management
- Integration with ERP and e-commerce systems
Some functionalities
- the system autonomously manages the activation of withdrawals with logics definable by the user
- cross-docking management
- shelf-life management, with full management of batches, batch characteristics, supplier batches
- batch and/or location reservation logics, Loading Unit management
- statistics of logistics activities and analysis of goods movements, monitoring of warehouse performance
- integration with automated warehouses
- logistics management of customizable products in acceptance and dispatch
- purchase planning and analysis of supplier’s orders with predictive algorithms
- returns management (reverse logistics)
- batch picking management or with contextual pick/pack to manage several shipments with few packages
- management of »fine« traceability: management of serial numbers and product serialization.
Target group
Footwear and accessories, furniture, food industry/food & beverage, paper/cardboard, packaging, pharmaceutical and cosmetics, consumer goods, mechanics/automotive, spare parts, tyres, high-tech electronics, appliances, furniture hardware and tools/DIY, hazardous goods and chemicals.
In general, all manufacturing and/or commercial/distribution industries.
Operation area
Acceptance, storage, quality check, picking, delivery, packing area.
Quarantine management, reservation area.
Features
- it is the system that shapes itself according to the type of operation and not vice versa
- quick integration with major transport providers
- customizable integration of logistics flows with subcontractors
- automated planning and analysis of customer delivery date based on order portfolio
- WMS activities of picking, receiving, storage, and transfers customizable according to logistics and company flows
- complete digitalization of incoming goods process through the Receipt of Incoming Goods
- Integration with Pick-To-Light on shelves or on cart with “Led-light” for the multi-order and/or multi-customer order-fulfillment with the following ventilation of picked goods
- use of heterogeneous devices (gun barcode reader, wearable, ring scanner, etc.) according to the ergonomics requested by the operator.
- high configurability of activities and flows related to the management of incoming and outgoing goods, as well as to the internal goods handlings
- purchase planning with demand driven models to “fix” forecasts (Forecasting purchase orders).
Product roadmap
Release v 1.20. Rev. 2 last quarter – Q4 2022
- Query optimization for analysis of historical warehouse data
- Extension of the multi-factory customer order portfolio plan
Pricing
Project/ One time license cost or in Saas modality/ Annual maintenance and update fee.
Product Flyer
Show news and articles in the following languages only





News
Obiettivo 2024? La logistica ecommerce (05.02.2024)
Stockforce WMS validato anche nel 2023! (17.10.2023)
WarehouseNavigation e WMS: ottimizzazione logistica interna (10.10.2023)
WarehouseNavigation e WMS: ottimizzazione logistica interna (10.10.2023)
[Evento] Quote-to-Cash and Motion-Mining® technologies. (04.10.2023)
Come snellire e digitalizzare i processi con WMS e MES (25.07.2023)
Logistica per l’e-commerce (30.11.2022)
Data di scadenza, termine minimo di conservazione, vita del prodotto. (16.09.2022)
Location and contact information
MOX Solutions srl Via G. Marconi 21/C 31030 Castello di Godego Italy UE, Extra UE https://www.moxsolutions.it/Federica Bergamin Marketing Manager info@moxsolutions.itTelephone: 0423722719 |